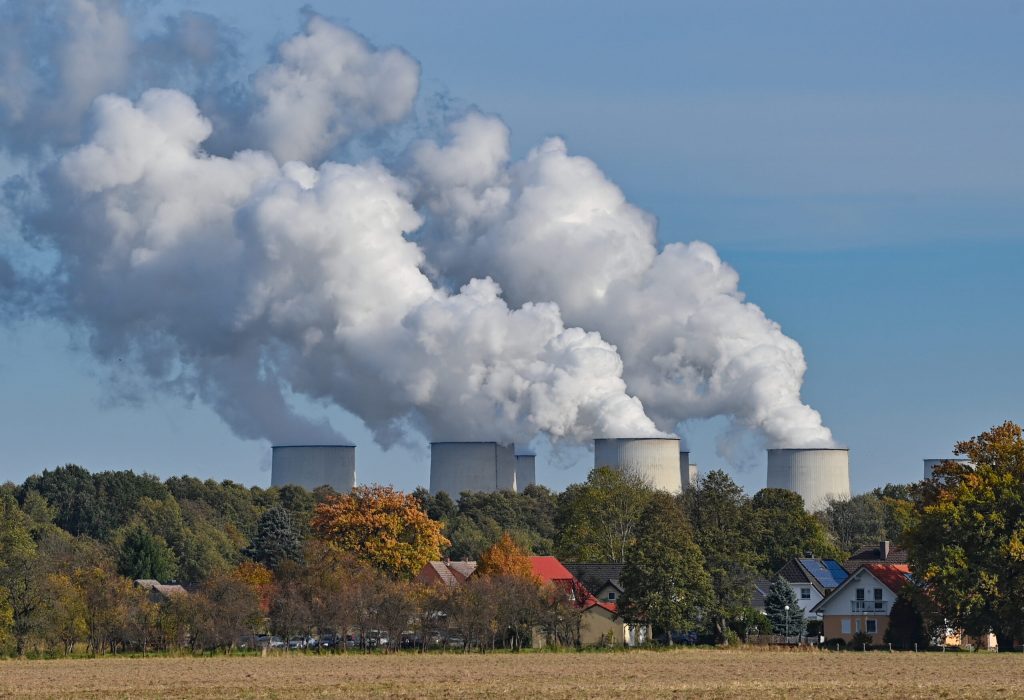
Designing a Future-Proof Carbon Capture System
In the near future, implementing a carbon capture system will become essential for various industries that generate significant amounts of carbon dioxide. This necessity arises not only from environmental demands but also from impending government regulations that will impose heavy taxes on emissions, making such systems nearly obligatory.
Furthermore, companies that adopt this technology early will likely gain a competitive edge in the market. However, the critical question remains: how can you ensure that your carbon capture system today will fulfill the requirements of tomorrow?
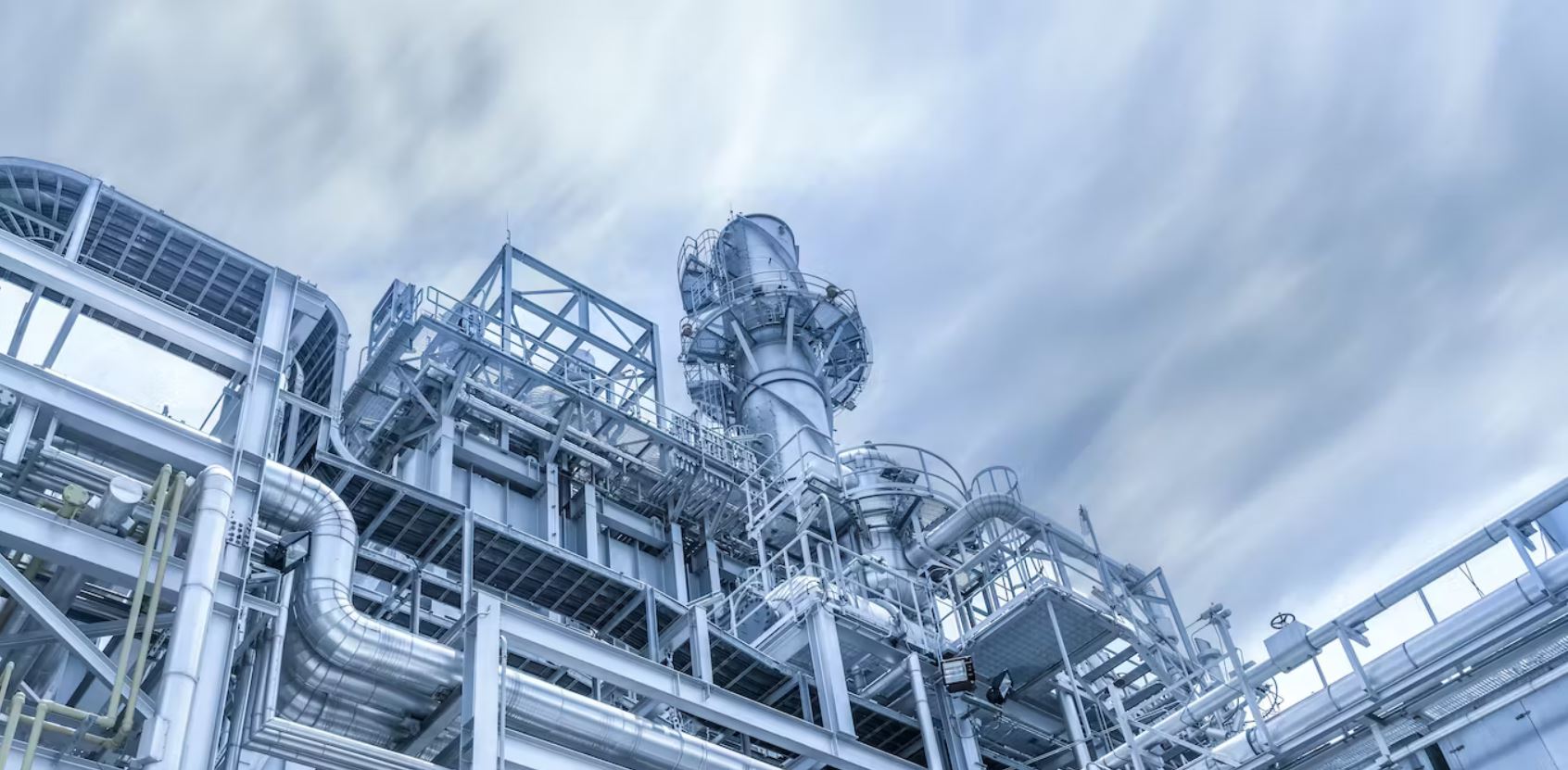
Key Factors: Efficiency, Reliability, and Modularity
Let’s examine the compression component of a carbon capture system. In this context, three factors—efficiency, reliability, and modularity—are crucial for making an installation future-proof.
First and foremost, while capturing carbon is vital for a sustainable planet, it is equally important to prevent emissions from occurring in the first place. Consequently, prioritizing efficiency becomes imperative. An operation that minimizes energy consumption not only helps the environment but also positively impacts your financial performance. Energy expenses can account for up to 80% of the total ownership cost of a CO2 compressor. Therefore, selecting an efficient model will yield quick returns on investment.
When choosing the appropriate compressor type, understanding the intended use of the compressed carbon dioxide is essential. For instance, liquefaction requires different outlet pressures compared to carbon sequestration. Additionally, the flow rate of carbon dioxide-rich gas plays a critical role. Below, we will explore various types of compression systems that enhance installation efficiency.
Types of Compressors in a Carbon Capture System
Generally speaking, if high pressure is required and the flow rate is moderate, a reciprocating piston compressor is the ideal choice. Conversely, if the flow rate is high but the pressure needs are lower, a screw compressor typically performs better.
One often overlooked factor contributing to system inefficiency is leakage. In the case of compressed air, leaks primarily waste energy. However, in carbon capture systems, leaks also have detrimental environmental effects. Moreover, any CO2 that escapes through leaks represents lost revenue for companies that sell their compressed gas.
Here’s a helpful tip: when selecting your CO2 compressor, consider investing in a model equipped with a variable speed drive (VSD). These compressors are among the most efficient available because they adjust their output to match demand, making them an optimal choice for operations with fluctuating flow rates.
The Importance of Reliable Carbon Capture Systems
Capturing CO2 emissions is a continuous process. If your facility operates 24/7, your carbon capture system must do the same. The consequences of a system failure can be severe, impacting both the environment and your operational costs. This reality underscores the importance of reliability. If your system malfunctions, the only destination for the carbon dioxide is the atmosphere.
Reliability is even more critical because compressing carbon dioxide is more challenging than compressing air. The presence of contaminants and the potential formation of carbonic acid when CO2 comes into contact with water can lead to corrosion.
Therefore, it is unwise to choose a CO2 compressor that is merely a modified compressed air unit. Always ensure that the manufacturer utilizes stainless steel or other corrosion-resistant materials.
Keep in mind that selecting the right compressor not only extends its lifespan but also reduces maintenance costs.
A Modular Carbon Capture System: A Strategic Decision for the Future
Implementing a modular carbon capture system is a smart strategic choice, especially when reliability is a priority. By distributing the workload across multiple compressors, you can ensure that if one unit fails, you can avoid releasing CO2 into the atmosphere.
Additionally, investing in a smaller standby model enhances the entire system’s scalability and simplifies maintenance. This proactive approach not only prepares you for unexpected issues but also streamlines operations.
Another key benefit of a modular carbon capture system is the flexibility it offers in technology selection for different stages of the carbon capture process. For instance, you might opt for a screw compressor in scenarios involving low pressure and high flow, while a reciprocating piston compressor would be ideal for situations with small flow and high pressure. This strategic pairing enhances the overall reliability of the system and provides greater adaptability to varying operational needs.
However, when integrating different technologies, it’s crucial to source all units from the same supplier. This practice minimizes compatibility issues and ensures seamless operation.
Choosing Atlas Copco as your supplier brings additional advantages, such as access to advanced central controllers. These controllers can significantly enhance both efficiency and reliability. Moreover, you will benefit from Atlas Copco’s SMARTLINK technology, which offers comprehensive monitoring and control capabilities.
Rely on Experts for Your CO2 Capture System
To design a carbon dioxide capture system that stands the test of time, it’s essential to consult with experts in the field. If you prioritize efficiency, reliability, and modularity, only equipment specifically engineered for CO2 compression will meet your needs effectively. If you want to learn how we ensure that today’s carbon capture systems are equipped to handle tomorrow’s challenges, reach out to one of our specialists today.